New series of Hydraulic Crawler Drill "HCR L100-E3" for emerging countries launched
Reduced fuel consumption and high drilling performance
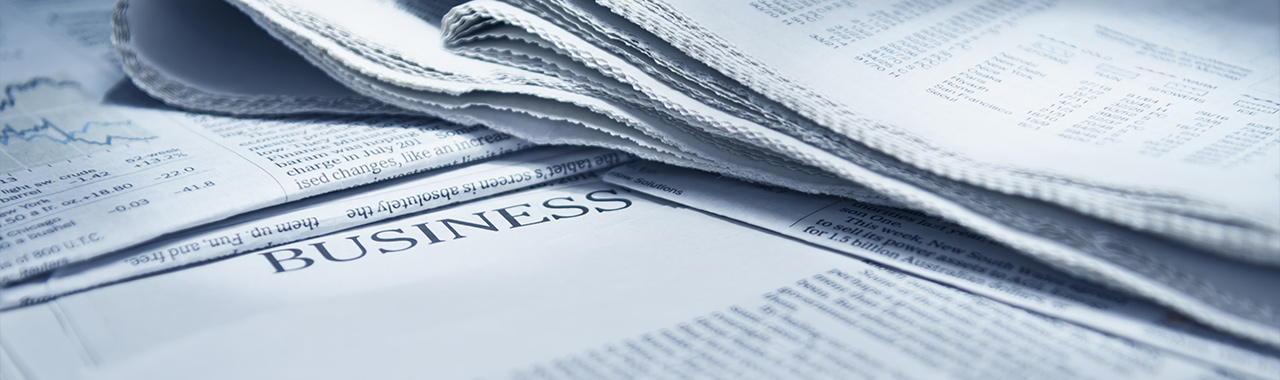
Reduced fuel consumption and high drilling performance
Furukawa Rock Drill offers the "HCR Series" of hydraulic crawler drill as its main products. Among the HCR Series, the current product "HCR1500-EDII," which is capable of drilling large holes with a maximum hole diameter of 127 mm, has been used mainly in limestone mines, nonferrous metal mines such as gold and silver mines, and iron ore mines. In recent years, the price of resources has skyrocketed against the backdrop of the Covid-19 disaster and other factors, increasing demand for the "HCR1500-EDII," which can be expected to increase production volume more efficiently. Furukawa Rock Drill has developed the a new series of hydraulic crawler drill as a successor to the "HCR1500-EDII," in order to further reduce fuel consumption and improve drilling performance.
The "HCR L100-E3" is equipped with the latest model engine (high output electronically controlled diesel engine) equivalent to Tier 3 emission regulation compliant, and the cutting-edge fuel-saving technology "Super Economy Mode PLUS [see Feature (3) below]" reduces fuel consumption and is environmentally friendly by selecting the appropriate engine speed according to rock types.
Furthermore, the semi-automatic drilling control iDS (Intelligent Drilling System) [see Feature 4 below], which automatically controls optimal drilling conditions according to changes in rock quality, has enabled smoother drilling, reduced hole deviation, which is a factor in deteriorating production efficiency, and extended the service life of drilling accessories. The company plans to market this product in emerging markets such as Southeast Asia and Africa, as well as in Oceania.
Furukawa Rock Drill will continue its product development efforts and further strengthen its lineup of the "HCR L Series," a new series of hydraulic crawler drills, to contribute to infrastructure development in Japan and overseas.
Equipped with hydraulic drifter HD715
The dual damper mechanism* and wedge-shaped piston shape with extreme energy transfer efficiency enable quick response to a wide range of different rock types. High crushing efficiency is achieved by optimal control according to the load. No complicated operation is required, and stable and comfortable drilling is possible with no wasted power.
*The dual damper mechanism (shock absorber with special structure) presses the bit against the bedrock to reliably transfer the energy of the impact wave of the impact piston to the bit to crush the bedrock, enabling drilling with the proper thrust force.
Equipped with a state-of-the-art engine equivalent to Tier 3 emission regulation-compliant
Equipped with a high-output electronically controlled diesel engine equivalent to Tier 3 emission regulation-compliant diesel engines, and equipped with a display device showing engine information as standard.
Super Economy Mode PLUS" cutting-edge fuel-saving technology
The engine speed during drilling (impact and blow operation) can be selected from four levels: 1600, 1800, 2000, and 2200 min-1. By selecting the appropriate engine speed according to the rock quality, this cutting-edge fuel-saving technology contributes to improved fuel efficiency while maintaining impact performance. (Patented)
A new system that adds "compressor/new unloading control" and "new auto throttle control" to the super economy mode has been added to further reduce fuel consumption.
New compressor unloading control
PLUS flushing-linked unloading control minimizes compressor standby power.
It is linked to the reduction of engine load to achieve low fuel consumption. (Patented).
New auto throttle control
PLUS a function that automatically controls engine speed in accordance with work.
This system reduces fuel consumption by automatically idling the engine when no work is being performed. (Patented)
Innovative "Semi-Automatic Drilling Control iDS (Intelligent Drilling System)
iDS (Intelligent Drilling System), which automatically controls the optimal drilling conditions according to changes in rock quality, is standard equipment. In addition to the conventional anti-jamming function that detects abnormal rotational pressure and bit clogging and automatically retracts the rock drill, an auto-feed stop function has been added to reduce hole deviation and extend the life of drilling accessories even further.
Comfortable cabin & spacious operating environment
The cabin, which offers spacious visibility in all directions, is equipped with ROPS/FOPS specifications. In addition, an outside air intake type air conditioner, which maintains a comfortable interior environment, is standard equipment. The airtightness of the cabin ensures comfortable work under a wide variety of operating conditions.
Semi-automatic type rod changer
A semi-automatic rod changer is equipped to continuously perform a series of complex operations from "addition" to "collection" of rods by simply pulling down one rod changer control lever in one direction. Speedy movements shorten the cycle time.
Model | HCR L100-E3 |
---|---|
Operating weight | 17,370 kg |
Drifter | HD715 |
Engine | Caterpillar C9.3B 280kW/2200min-1 |
Compressor | Airman PDSF290 13.5m3 1.03MPa |
Rod changer | GR802 12ft T51 6 pcs+1 (Starter rod) |
Drilling diameter | Φ90~127mm |